On a roll: Trinidad Tissues grows into a zero-waste company
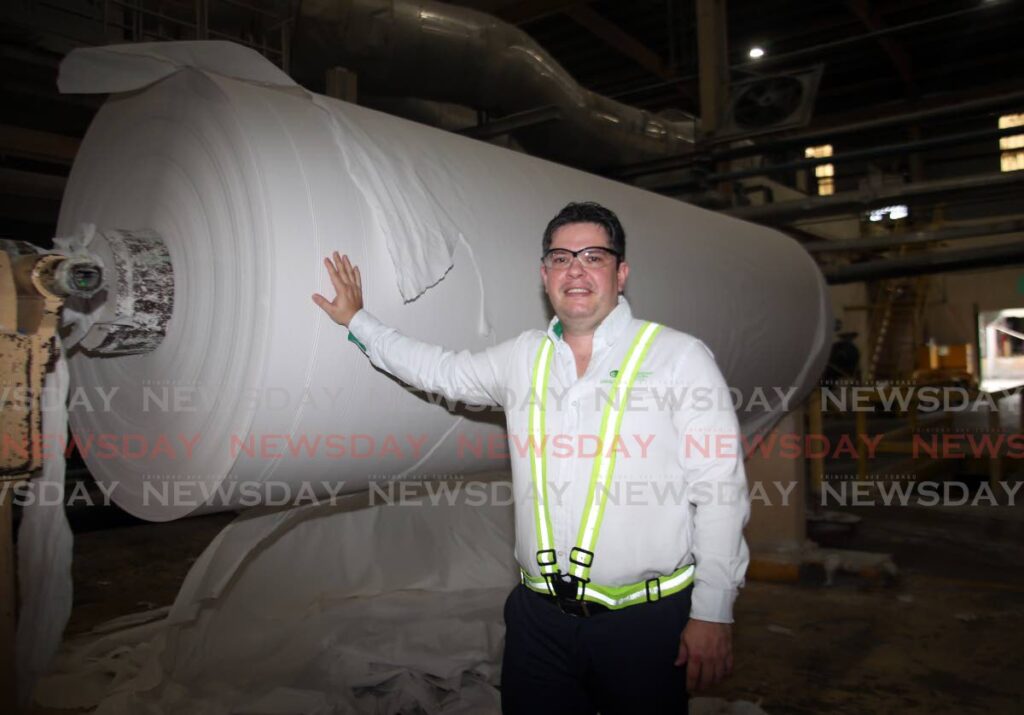
Trinidad Tissues Ltd (TTL) did not grow overnight.
Country manager Bernard Hoeger said upon his entry to the country from Venezuela, in 2009, he began working for the Grand Bay Group, a Panama company that owned and operated a paper mill in Arima. The mill – Grand Bay Paper Products (GBP) had a lot of problems.
The manufacturing operations faced bankruptcy. The majority of employees were expatriates as the locals did not have the expertise to run the paper mill which was and still is the only one in the English-speaking Caribbean.
But Grand Bay Group was interested in another company – TTL – for which Hoeger and his team negotiated its acquisition.
At the time the companies were at separate locations. The GBP paper-manufacturing operations were at Arima and the TTL converting operations were at Trincity.
GBP workers weren’t accustomed to working with a lot of high-quality machinery. They had a combined marketing distribution, so they were not focused on the converting process, which was TTL's strength. A decision was made to merge the companies under Grand Bay TTL but based in Arima.
Part of that growth was establishing all the quality controls, developing the stock-keeping units, eliminating what was not needed.
“We had to do a quick turnaround, but in order to do that, the group decided that it was not enough to just purchase the tissue machinery, we needed to have brands established and converting processes as well. So, we decided to invest,” he said.
“That way, we will have the tissue machine placeholder and converting placeholder brands that have been in the market for years, which was a very wise choice.”
He explained that rejected toilet paper or paper towels are recycled to be made into useable products. Hoeger boasted that TTL is now a zero-waste company.
“If it's a reject it’s a reject, we cannot sell cheaper,” he said.
He added that even though this is the case, the rejected paper is processed again and repurposed into useable toilet paper or paper towel rolls.
Back in 2009, many of the workers at the factory didn’t even have work permits, he said.
Hoeger told Business Day that when he and his team from Panama took over, there were no local supervisors and no supervisors on the tissue side of the business.
“They lacked safety, a job safety analysis, they lacked a lot of OSHA (Occupational Safety and Health Act) follow-ups, no reporting structure, there were no guidelines regarding standards.”
Hoeger said there was a lot of work to be done on the company including developing the standard operating procedures. He said this included ensuring that the water used in the factory was clean and can be used to transform the recycled paper into sludge to create useable hygienic products.
The company now has a workforce of 380 full-time employees with the purpose of manufacturing, converting and selling hygienic tissue papers to TT and other countries in the Caribbean. TTL’s headquarters are in Panama with sister companies based in Colombia, Guatemala and Venezuela.
Hoeger said, “We can boast of having the only tissue paper mill and the largest paper converting plant in the English-speaking Caribbean.”
Hoeger added that while TTL is now only able to recycle a small amount of toilet paper, from January 16, the company will align itself with different companies in Colombia which would have different uses for the waste material.
“They have chicken bedding; they can make blocks and cement from that sludge. That would reduce our footprint further by 20 per cent if we manage to convert all that organic material into something useful,” Hoeger said.
Hoeger said by the second quarter the company hopes to start utilising the organic material.
Business Day got a tour of TTL’s factory. Hoeger said the process entails putting enormous rolls of what they call “parent rolls” in a machine called the rewinder.
“The roll gets unwounded, put into a lab and cut down to the size required by the consumers and then it’s repacked by the packing machines.”
Production superintendent of the mill Iram Ali, responsible to produce the semi-finished rolls, explained that the process includes cleaning and screening equipment in the de-inking plant, water treatment systems, the paper machine and rewinder.
“The raw material is disintegrated by a pulper and cleaned of any contaminants. The pulp slurry is sprayed onto a forming fabric where the paper web is formed and then dried to the desired moisture content. Jumbo parent rolls are re-wound on the rewinder and slit according to customer specifications. Effluent is sent to a treatment facility where it undergoes processing, dewatering via a screw press and is then safely disposed of at a local landfill site.”
Ali said the importance of the equipment is to ensure the tissue paper adheres to the hygiene guidelines, has the physical properties and the customer specifications.
“The various types of equipment contribute to minimising the overall impact on the environment in different ways. For instance, the paper making process is extremely water intensive. The need for fresh water is reduced through utilising the water clarification systems helping us to maintain a closed loop water circuit. Additionally, large amounts of recycled paper are consumed in the de-inking plant through cleaning and screening equipment thereby reducing the landfill volumes.”
Once the rolls are cut to the size found in people’s homes, the paper is sent to be printed.
Ever wondered how the toilet paper or paper towels got the imprints? Well, converting production manager Vindar Ragbir is responsible for that. During the tour, he told Business Day that a specific pattern is imprinted on the sheets to make it softer and more durable.
TTL is responsible for distributing to brands such as White Cloud, Soft ‘n’ Pretty, Soft Weave, Suave Ultra and So Soft.
Ali added that the process of recycling paper positively influences the environment, and this is evident by TTL’s latest achievement of winning the Green Manufacturer of the Year Award by the TT Manufacturers Association for the second time.
“What we did was change the UV lights which managed to consume around 4,000 tonnes of recyclable material, so that's a sort of waste. Instead of newspapers ending up in landfills, they are collected since we can use a portion of it here. We align ourselves with the local recycling company New Age Recycling Ltd,” said Hoeger.
New Age Recycling Ltd is a recycling company based in Arima. Hoeger said TTL adheres to the International Organisation for Standardisation (ISO) standards and was the first company to be FSC (Forest Stewardship Council) certified. FSC is an international non-profit, multi-stakeholder organisation established in 1993 that promotes responsible management of the world's forests.
Comments
"On a roll: Trinidad Tissues grows into a zero-waste company"