Of elephants, trains, snakes and planes
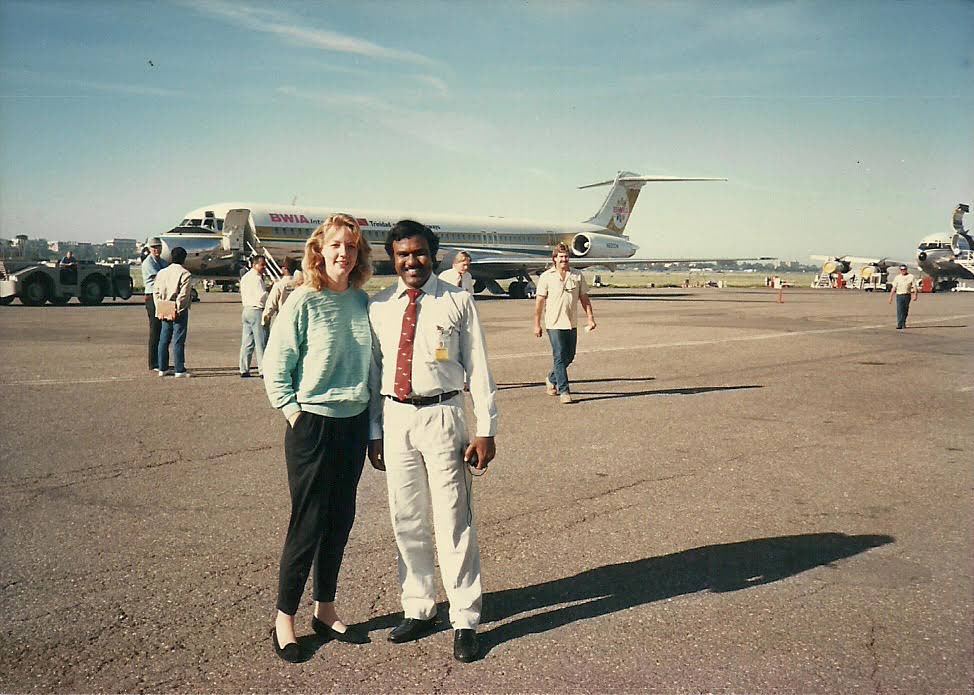
All commercial aircraft are designed, built, tested and certified in accordance with the international safety standards of ICAO Annex 8 – airworthiness.
Aircraft manufacturing countries have used the ICAO standards to develop their own airworthiness codes for aircraft manufacturing.
In the US, the airworthiness code is Federal Aviation Regulations Part 25 (FAR 25), while in the EU, the airworthiness code is Joint Airworthiness Regulations 25 (JAR 25), which is almost identical to FAR 25.
Most aircraft manufacturers in other parts of the world adopt the standards of FAR 25 and JAR 25.
In this way, the certification of foreign-built aircraft in the US and the EU is made easy.
Before the completed aircraft certificate of airworthiness can be issued, it must be verified that all parts and materials used in the manufacturing of the aircraft comply with the applicable airworthiness and manufacturing regulations.
In addition, all the passenger-cabin materials such as seats, side-wall panelling, carpets and bulkhead tapestries must be tested for compliance with the applicable flammability regulations.
On June 2, 1983, an Air Canada McDonnell Douglas DC-9-32 aircraft operating a flight from the Dallas/Fort Worth Airport to Montréal-Dorval Airport developed an in-flight fire in a rear lavatory that spread between the outer skin and the inner decor panels, filling the cabin with toxic smoke. The fire burned through critical electrical cables, which disabled some of the instrumentation in the cockpit.
The aircraft made an emergency landing at Cincinnati/Northern Kentucky Airport. After it landed and the doors were opened, the heat of the fire and fresh oxygen from the opened exit doors created flashover conditions, and the aircraft's interior immediately became engulfed in flames, killing 23 of the 41 passengers.
This accident triggered a series of regulatory actions to increase the survivability of aircraft passengers and crew during an aircraft fire.
Consequently, US amended FAR Part 25 to prescribe more stringent flammability requirements for aircraft interior materials that lowered the heat release in the event of a fire.
BWIA was operating a fleet of McDonnell Douglas DC9-83 (MD 83) aircraft, which at that time was the most popular medium-range twin jet.
Douglas opened a second production line at its Long Beach, California facility to cope with the large backlog of MD83 orders.
In 1988, BWIA entered into a lease agreement with the International Lease Finance Corporation (ILFC) for an MD83 aircraft Manufacturer’s S/N 49824.
In the same year, I attended a meeting at the Douglas facility along with the vice president, technical, of BWIA, to discuss the new flammability requirements for tapestries that were to be installed on all the interior cabin bulkheads.
We met with Douglas’s industrial design personnel, who advised that during testing, the machine-woven tapestries did not meet the new flammability requirements, and only hand-woven ones from India passed the tests due to the tightness of the hand-weaving. We signed off on the samples of the Indian hand-woven tapestries in the BWIA livery.
To accelerate MD83 aircraft deliveries, Douglas would fly aircraft to Tracor Aviation in Santa Barbara, California, for the installation of the seats, galleys, closets, carpets, tapestries and final certification. When MD83 aircraft S/N 49824 arrived at Tracor Aviation, I was assigned to oversee the final completion and certification.
I arrived in Santa Barbara on December 31, 1988. There were daily production meetings to status the work progress of all aircraft, during which all outstanding items would be discussed.
Work was progressing well with the BWIA MD83, and the meetings will note the “tapestries en route from India” – until it was discovered that the whereabouts of the tapestries was unknown.
This situation had the potential to delay the aircraft certification, and I demanded an explanation from the Douglas programme director.
He then informed me that the agent for the tapestries in Los Angeles would communicate with Raju, who manufactured the tapestries, through a customs officer in Mumbai acting as a middleman.
A fax with orders would be sent to the customs officer, who would travel in his jeep to Raju’s village to make payments and collect finished products for shipping to Los Angeles.
Raju travelled around on an elephant. One day, while they were crossing a rail track, a train collided with the elephant, injuring Raju and killing the elephant.
Raju was laid up in hospital for six weeks and the customs officer was unable to contact him. At that time, communications were quite challenging, as mobile phones and the internet were non-existent.
The programme director was unable to provide a delivery date for the tapestries. As a contingency measure, it was decided to install the decorative panlam used on the overhead bins on all the cabin bulkheads. Before the panlam could be installed, it had to undergo flammability testing to demonstrate compliance with the regulations.
An FAA-approved test plan had to be developed, the burn testing of samples had to be witnessed by the FAA and the test report had to be approved by the FAA.
It was estimated this testing would delay the aircraft delivery by at least three weeks.
I called the BWIA VP to brief him on this new development and began by saying, "I want to let you know that the aircraft will be delayed by three weeks because Raju, who manufactures the aircraft tapestries, travels around his village on an elephant. One day, while crossing a rail track, a train collided with the elephant, killing it and injuring Raju." Before I could finish giving the reasons for the aircraft delay, the BWIA VP, using the most colourful expletives, retorted, "What nancy story are you telling me?" and hung up.
The Douglas programme director immediately sent an official letter to the BWIA VP by fax explaining the reason for the tapestries' delay.
He called back shortly afterwards and apologised for his earlier outburst.
The BWIA VP travelled to Santa Barbara in April 1989 for the aircraft delivery. During delivery functions, he would have me tell the story about the slow elephant that delayed the aircraft certification. I would embellish the story by adding that the customs officer would travel through the jungle in his jeep and give the fax to a cobra, which would slither through the village and deliver the fax to Raju.
Comments
"Of elephants, trains, snakes and planes"