Evolution of the jet engine
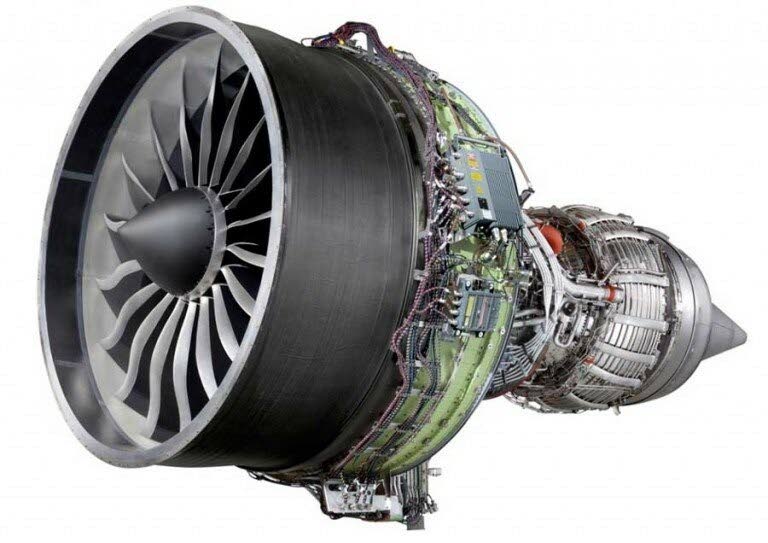
Today, most large commercial aircraft are powered by jet engines: hence the term "jet aircraft."
The jet engine is a far cry from the piston engine, which powered the Wright Flyer on December 17, 1903, whichheralded mankind’s historic first powered flight.
Aircraft jet engines use the principle of jet propulsion, that is, the propulsion of an object in one direction produced by ejecting a jet of fluid in the opposite direction.
The moving body is propelled in the opposite direction from the jet, based on Newton's third law of motion: "For every action (force) there is an equal and opposite reaction."
All jet propulsion engines are known as reaction engines.
The principle of jet propulsion dates back to the aeolipile, a device described by Hero of Alexandria in first-century Egypt.
The aeolipile consisted of a spherical vessel with oppositely bent or curved nozzles projecting outwards. When the vessel is filled with water and heated, steam is expelled out of the nozzles, which generates thrust thanks to the reaction principle based on Newton's third law of motion causing the vessel to rotate.
Rocket engines are reaction engines, producing thrust by ejecting gases rearward, in accordance with Newton's third law.
Most rocket engines use the combustion of reactive chemicals to supply the necessary propulsive force.
Rocket engines are commonly used by ballistic missiles to launch space vehicles. They carry their own oxidisers, unlike most combustion engines, and can be used in a vacuum to propel spacecraft and ballistic missiles.
The first working pulsejet was patented in 1906 by Russian engineer VV Karavodin, who completed a working model in 1907.
The French inventor Georges Marconnet patented his valveless pulsejet engine in 1908 and Ramon Casanova, in Ripoll, Spain, patented a pulsejet in Barcelona in 1917, having constructed one in 1913.
Robert Goddard invented a pulsejet engine in 1931 and demonstrated it on a jet-propelled bicycle.
Engineer Paul Schmidt pioneered a more efficient design based on modification of the intake valves, earning him government support from the German Air Ministry in 1933.
A pulsejet engine is a type of jet engine in which combustion occurs in pulses. A pulsejet engine can be made with few or no moving parts, and is capable of running statically without having air forced into its inlet. The best-known example is the Argus As 109-014 used to propel Nazi Germany's V-1 flying bomb during World War II.
Since the 1930s, aerospace engineers realised that the maximum performance of piston engines was limited, as propulsive efficiency declined as blade tips approached the speed of sound.
For engine performance to increase beyond the sound barrier, a radically improved piston-engine design was required, or a new type of propulsive engine powerplant would have to be developed. This led to the development of gas turbine engines.
The Heinkel He 178 was an experimental aircraft designed and produced by the German aircraft manufacturer Heinkel. It was the world's first aircraft to fly using the thrust from a jet engine.
Unlike piston engines, which have four cycles in sequence – intake, compression, combustion and exhaust – jet engines are continuous cycle engines, in that all four cycles take place at the same time. Jet engines have axial flow compressors, which increase the pressure of the air from the intake. The compressed air is mixed with fuel in the combustion section, where there is continuous ignition. The exhaust gases impinge on high-pressure and low-pressure turbine wheels which drive the compressor and the intake fan respectively.
The rearward acceleration of air by the intake fan and the exhaust gases creates an opposition reaction which thrusts the aircraft forward.
Fuel represents approximately 40 per cent of an airline's variable costs. Therefore, airlines seek to acquire aircraft with highly fuel-efficient engines.
Accordingly, engine manufacturers are continuously engaged in research and development to produce engines that can provide a competitive thrust-specific fuel consumption (TSFC).
TFSC is the mass of fuel needed to provide the net thrust for a given period – pounds of fuel per hour-pound of thrust.
Today, most jet engines are high-bypass turbofan types, where a single fan driven by the core engine accelerates a large volume of air rearwards, creating approximately 75 per cent of the engine’s thrust.
The addition of the fan minimally changes the fuel flow rate for the engine's core, causing a turbofan to generate more thrust for nearly the same amount of fuel used by the core.
This means that a turbofan is very fuel-efficient. High-bypass-ratio turbofans are nearly as fuel-efficient as turboprops. Because the fan is enclosed by the inlet and is composed of many blades, it can operate efficiently at higher speeds than a simple propeller. For this reason, turbofans are found on high-speed aircraft and propellers used on low-speed aircraft.
Aircraft manufacturers offer airlines engine options based on the operating experience of an engine already used on another aircraft type.
In this case, the aircraft is manufactured with a standard engine interface to allow for interchangeability of engines.
On the Boeing 787 Dreamliner, there are two engine options – the General Electric GEnx and the Rolls-Royce Trent 1000 – and each type can develop between 55,000lb and 70,000lb of thrust.
On the Airbus A320neo, there are two engine options – the CFM International LEAP-1A and the Pratt & Whitney GTF (PW1100G) – with 20 per cent lower maintenance cost than current A320 engines.
The Boeing 747–8 has 4 General Electric GEnx-2B67 Turbo-Fan Engines. The older models of the 747s offered the Pratt & Whitney JT9D, the GE CF6 and the Rolls-Royce RB211 engines.
The Boeing 737 MAX 8 aircraft is powered by the CFM International LEAP-1B engine.
The sales contract for most aircraft contains performance guarantees relating to fuel burn. If the aircraft is not meeting the performance guarantees, the aircraft manufacturer will have to take corrective action and/or provide compensation to the airlines.
Jet-engine technology is constantly evolving. At present, aircraft and engine manufacturers are collaboratively developing the technologies to transition to sustainable fuel to meet global aviation-emissions targets by 2050.
Comments
"Evolution of the jet engine"