Aircraft maintenance: All about the spare parts
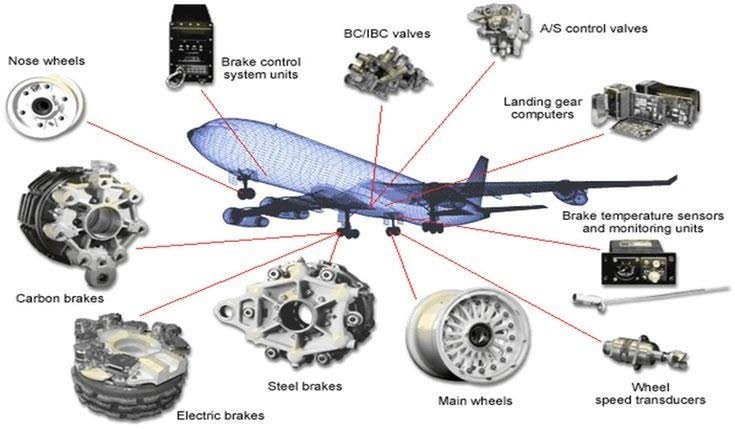
Part III
The integrity of aeronautical products such as aircraft spare parts is critical for the continuing airworthiness of an aircraft. Defective components must be replaced during the maintenance process with an approved spare part.
Aeronautical products fall into three main classes and are procured from manufacturers approved by the aeronautical authorities, and known as the original equipment manufacturer (OEM). Parts manufactured by OEMs are designed to fit the parts being replaced, in every sense of the word “fit.” This means the replacement part must serve the same exact purpose as the original part used during the testing and certification of the aircraft.
A class I product is a complete aircraft, engine or propeller which has been type certificated in accordance with the appropriate airworthiness requirements and for which the necessary type certificate, or equivalent, have been issued.
A class II product is a major component of a class I product such as a wings, empennages, landing gears, hydraulic pumps, starters and flight controls etc.
A class III product is any part or component which is not a class I or class II product including standard parts.
A standard part is manufactured in compliance with a specification approved by airworthiness authorities including the design, manufacturing, and uniform identification requirements. Nuts, bolters, washers and rivets are standard parts.
All aeronautical products are accompanied by airworthiness approval tags issued by the OEMs attesting to its conformity with the approved manufacturing specifications.
Aircraft maintenance organisations (AMO) have a "bonded area" with systems and procedures for the handling of aircraft spare parts.
All incoming aircraft spares parts are routed to a designated area called "receiving inspection" where the parts are inspected by qualified inspectors for any signs of obvious damage. The airworthiness approval tag is scrutinised to ensure that the part number and/or the serial number matches the component and appropriately certified. Upon satisfactory inspection of the part, a "serviceable tag”, normally with a green band and a QR code, is attached to the part containing the description, part number and/or model number, serial number and signed and dated by the receiving inspector. The part is then released for storage in another designated area.
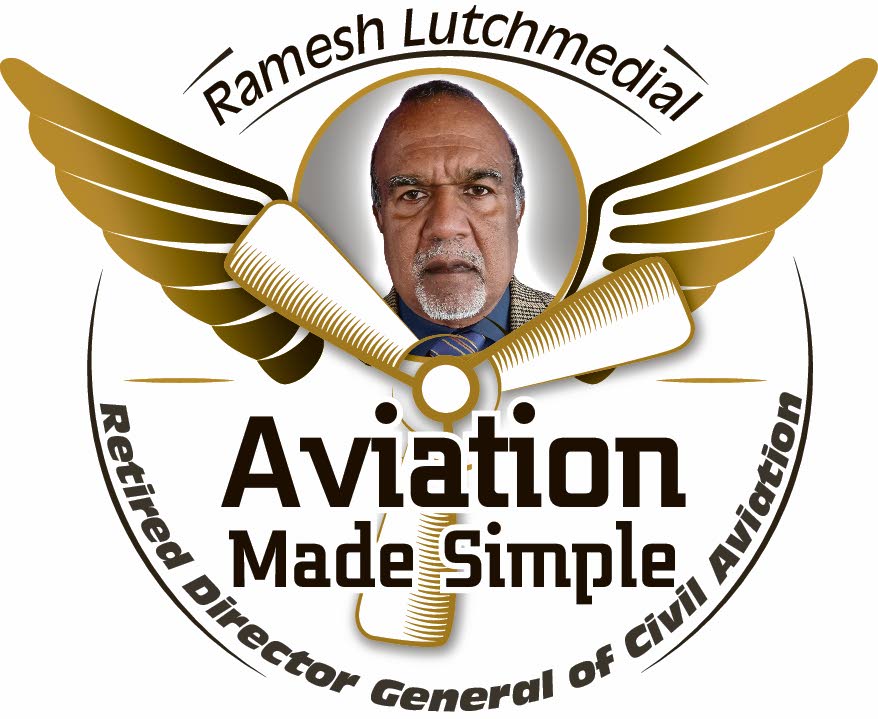
Parts that are damaged or missing its airworthiness approval tag are routed to a quarantine area for shipping back to the OEM for repair and/or re-certification.
An "unserviceable tag", normally with a red band, is attached to all defective components removed from an aircraft containing the description, part number and/or model number, serial number, reason for removal and signed and dated by the person removing the part. The part is then routed to a designated area for unserviceable parts.
All serviceable aircraft parts must be stored in a "controlled" environment.
Aircraft tyres are stored in dry, dark areas as exposure to sunlight, ozone and high ambient temperatures contribute to the deterioration of the tire threads and sidewalls.
Avionic components are stored in an area where the humidity and temperature are controlled to prevent damage that can be caused by moisture and high temperatures.
A major issue plaguing the aircraft maintenance industry is bogus parts which is a growing problem. Bogus parts range from uncertified counterfeit parts to time expired parts which are recycled and sold to AMOs.
Aircraft landing gears and engines discs on which the compressor and turbine blades are mounted all have a finite life based on landings and/or flight hours. Once the finite life is reached, the parts must be discarded, even though there are no signs of obvious damage. However, some of these discarded parts are illegally recycled by unscrupulous entities.
Counterfeit parts are fake replications of a part using inferior materials and sold under the brand of an approved OEM.
In 1995, American Airlines flight 965 crashed on approach into Cali, Colombia. Before air accident investigators could examine the wreckage, 523 of items including cockpit avionics, engine-thrust reversers, and other parts were removed by scavengers from the crash site using a helicopter. Many of the stolen parts later appeared for sale in the Miami area. American Airlines responded by publishing a list of the parts missing from the crashed aircraft, including the part numbers and serial numbers.
During the investigation of aircraft accidents, the source of parts that are suspected of contributing to the accident are fully traced back to its origin by the accident investigators.
On September 8, 1989 Flight PD 394 operated by Norwegian charter airline Partnair using a Convair CV-580 crashed off the coast of Denmark, killing all 50 passengers and five crew members on board.
The accident was investigated by the Norwegian Safety Investigation Authority (NSIA). The NSIA determined that the accident was caused by loss of control due to the destruction of primary-control surfaces in the tail section caused by vibrations due to abnormal clearances in the vertical stabiliser attachments to the fuselage structure.
The abnormal clearances in the vertical stabiliser attachments were caused by excessive wear in the pins and sleeves used in this structural joint. During the traceability of the pins and sleeves by the NSIA, it was determined that three pins and sleeves were counterfeit parts installed on the aircraft during a previous maintenance check. They were incorrectly heat-treated during manufacture and could only bear 60 per cent of the breaking strength.
Comments
"Aircraft maintenance: All about the spare parts"