Made868 facility helps designers move ideas to production
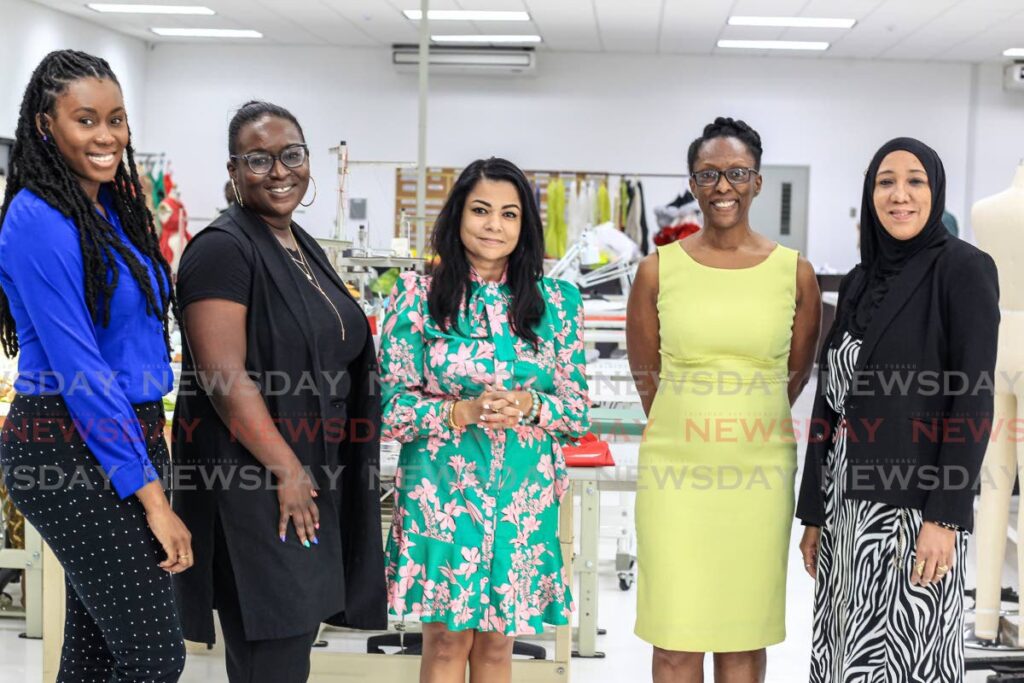
Creative people are plagued with the worry of making their ideas a reality along with marketing their products and ensuring their work gets the traction it needs.
But Made868 aims to reduce that stress.
The Made868 facility, set up by Sandra Carr, its supervisor, programme leader and senior lecturer at the Academy of Caribbean Fashion and Design, offers them the space to produce any and every idea they may have.
She said with great emphasis that everyone with an idea can use the facility, as it is not just for fashion designers.
Made868 is based at UTT's John S Donaldson Campus on Wrightson Road, Port of Spain.
Carr said with its state-of-the-art machinery, people in numerous branches of the arts have created products such as jewellery, plush toys, handbags and even plant pots. The services it provides include CNC milling with a computerised machine used to create woodwork, 3D signs and Carnival floats; laser cutting, which gives precise cuts or intricate engraving on acrylic, wood, metals and textiles; vinyl-cutting, which gives designers the chance to create their own banners; and 3D printing, which is used to materialise creations from earrings or coasters.
Carr said she hopes to get more creators to integrate technology into the process of production.
"You name it, whatever the creatives have envisioned, we have brought it to life. So people see that and they're very pleased with the quality of work. So...they are now saying, 'I can come, I can have all these dreams, I could create all these things – and now I can see them come to life.'"
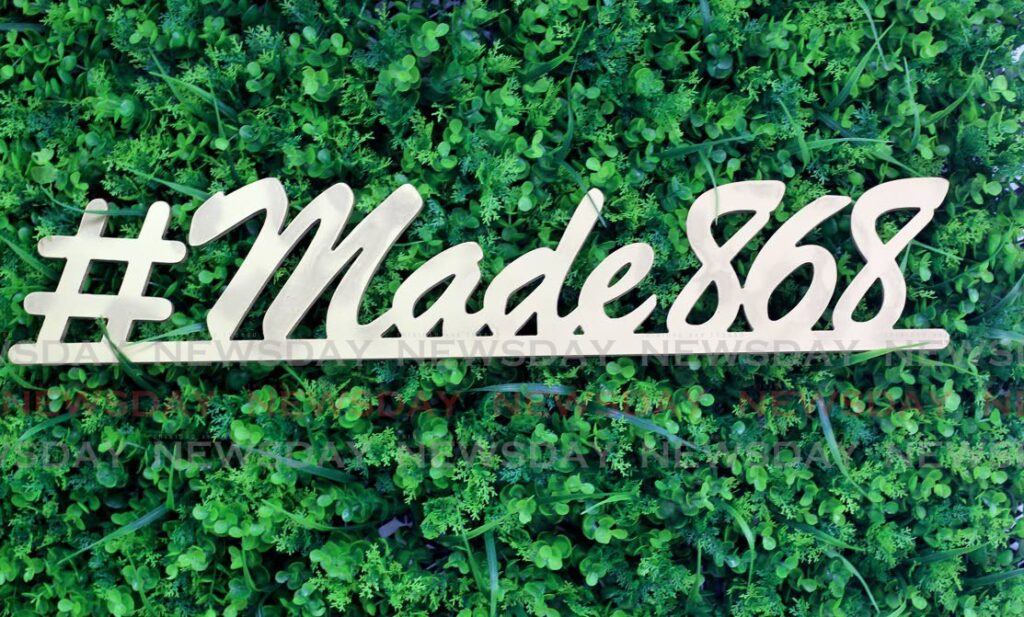
Carr added, "What we are telling designers is, 'Let us do your production for you.' Because the thing is, the way this industry is, designers do everything. They do the marketing, sewing, illustrations and stuff, so we're like: 'Focus on your target market, your marketing, and bring the production for us, because this way you can merge into new markets and still have the products so that you can cater to your target market.'"
Made868 was launched on January 17 with the idea of being a fashion hub for graduates of the academy.
"Initially we were looking at a fashion incubator, where the graduates will come into that for, like a year, develop their brands – then they will go out and then we would have another batch.
"But we saw there was a greater need, and in collaborating with FashionTT, there's a greater need to fill the gap in the industry to have manufacturing for the designers. So from that incubator idea came what we have today.
"The business model was actually devised as a three-year business model, where the first year we will cater to our local designers, the second year to regional designers, and then the third year to international designers."
Carr proudly revealed that the three-year business model was accomplished a mere two months away from Made868's first anniversary, and that word about the facility is getting out, which will lead to its expansion.
She also added that the facility has earned in excess of $300,000 in the ten months it's been in operation.
Designers who use the facility may have small or large orders to fulfil, and the cost is fluid, as it depends on the material, style and quantity.
General manager of FashionTT Lisa-Marie Daniel added that once FashionTT was started in March 2015, and several stakeholder consultations were held, the decision to create Made868 coincided with Carr's aims.
Daniel said, "We're hoping within a three-year period, according to the plan, it's self-sustainable and it can go off into its own private entity, which is managed and driven by its shareholders, and as such, supported by stakeholders, business-wise.
"But before that, this facility has the full support of the government of TT and UTT as the lead in anything that fashion has to do, to support as the business arm, in terms of making it successful over the next three years."
Carr said Made868 can only be a pilot project, since the facility is booked up until March next year, showing the need for expansion.
She explained the process with the help of the facility's manager Anna White.
White said any creative person with a idea in the form of a sketch, or not even that, can make an appointment to carry out the process, or just walk in and they will be attended to.
Carr said, "A designer can (and) we'll talk about the technical package, which is a blueprint of the design."
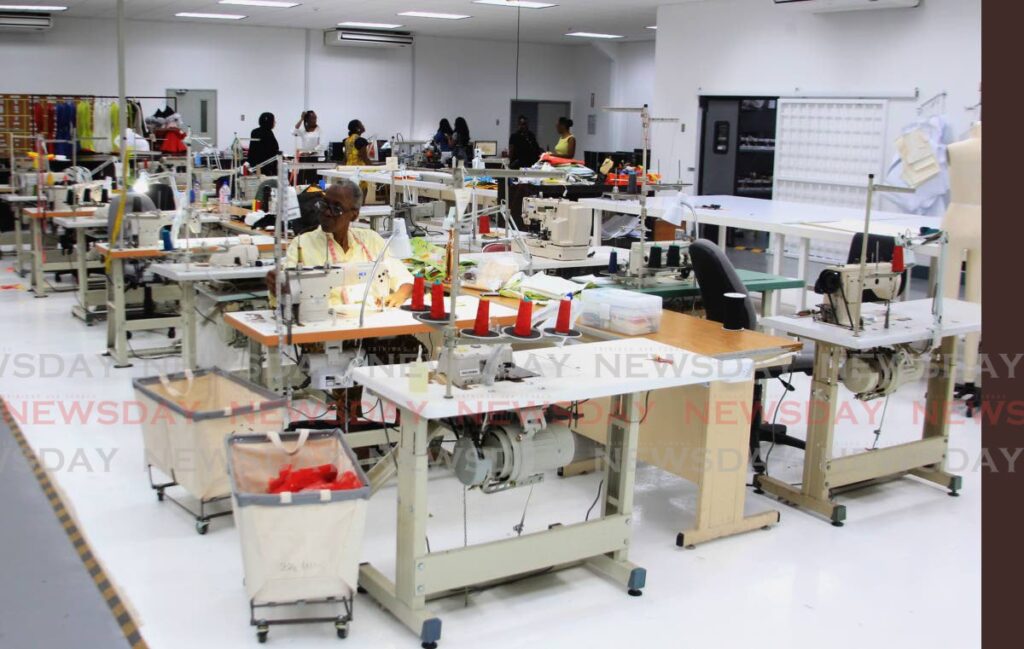
The technical package, or "tech pack," is a compilation of different fabrics, illustrations, stitch patterns and all other necessary material for the designers to make decisions on the design.
"Once that sample is okay with the designer, that sample then goes into production. So we're working with the designer to bring whatever they have envisioned to reality.
"So it's the first of its kind, and we hope that we will expand into more, because it's needed, and especially as we merge into the rest of the Caribbean and expand to the diaspora."
She said not only would it be easier for designers to get their work made and into the market, but it will be cheaper.
She added that even though it is affordable, the facility will only provide products that meet international standards, so that the creations can be recognised anywhere in the world and be comparable with international standards as well.
"It's much cheaper for designers to come here out of the US and do production. Nobody produces in New York, because it's too expensive, so with the exchange rate as well as the minimum wage, it will be cheaper for them to come here."
The minimum wage rate in the US is US$7.25, which equates to TT$49.23. Carr added that the facility was strategically placed near the port of Port of Spain,so there would be no high transportation fees.
Business Day was given a tour of the facility. When you enter Made868, you see a row of sewing machines, with threads intricately wound into the machines for the seamstresses and tailors.
At the time there was only one seamstress there, quietly working on a white piece of fabric.
At her side was Chioke Herbert, the fabric printer and technical specialist who is responsible for printing designs onto any type of fabric, using the HP Latex 360. This printer is big enough to take up almost an entire wall, and with the help of Herbert and his computer, the desired design can be pulled up and within seconds the printer begins to work on the chosen fabric, in any quantity. The time it takes to print can range from 15 minutes to several hours.
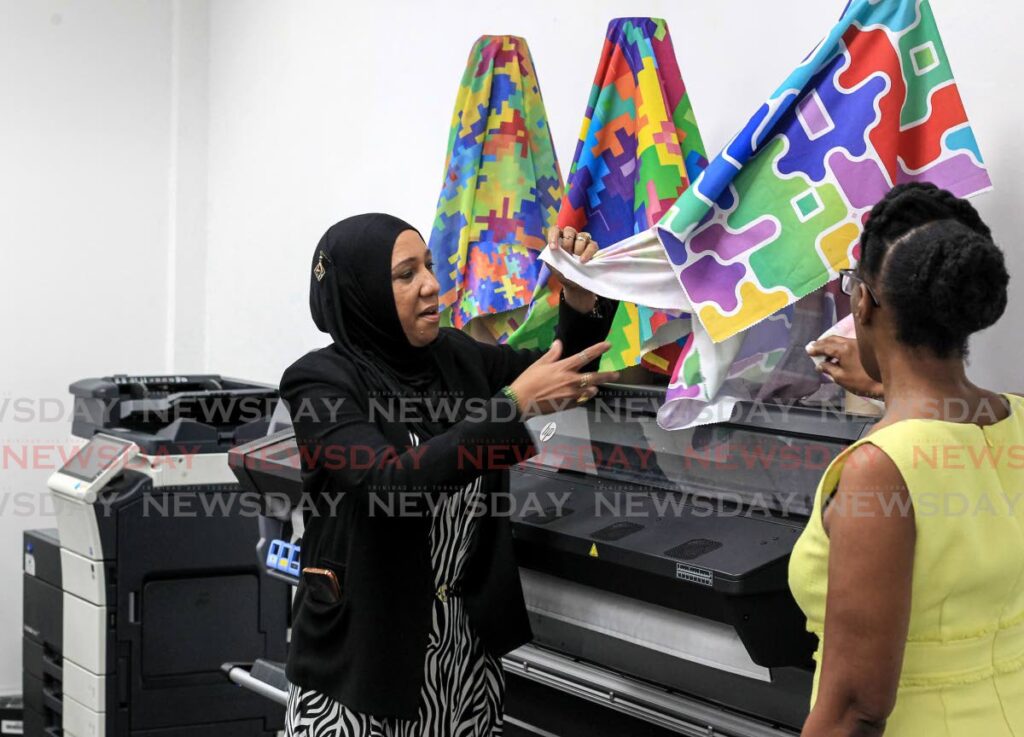
While walking through the facility, Carr showed us the photography room, which was adorned with handcrafted flowers and a backdrop of a waterfall which was used for Made868's networking event earlier this month. She explained that the room is used photograph finished designs, and even though it's a small room, it can become whatever the designer envisions. This is because designers are allowed to bring their own decorations, models and any prop they deem necessary to give the full effect of what their fashion line is offering to consumers.
At the back of the room, a 3D printer was working on producing a blue plastic coaster during our visit. Every designer is free to use it once their design in line with its services.
Next is a separate space for the laser cutter, which takes up the entire room and is handled by Elias Mitchell. This room has been dubbed the FabLab and Mitchell is the lab technician there. In this room, Mitchell places the chosen "canvas," whether plastic or wood, enters the design on a computer and the laser engraves it on the material.
The Made868 team urges designers at least to see the facility before working with them, but they are positive no one would be able to turn them down. Many designers have used the facility, among them Kimo and Tyshwn Mitchell, both new and upcoming designers, and even Rosalind Gabriel, a veteran in the industry, is currently using it to create her Carnival costumes for 2023.
Comments
"Made868 facility helps designers move ideas to production"