How positive leadership can revolutionise HSSE
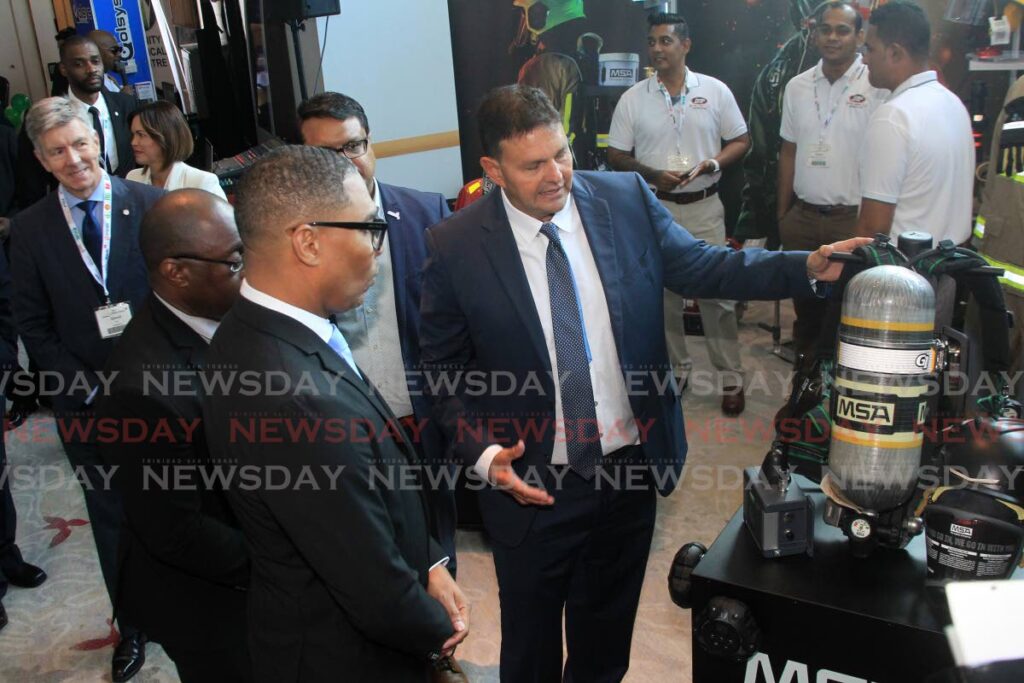
Safety is not the absence of accidents; it is the presence of capacity – and a key factor in building capacity in any part of a business, and most especially in the field of health, safety, security and the environment (HSSE), is positive, accessible and engaging leadership.
Bill Simms Jr, author of a must-read book on achieving sustainable behaviour change in teams in the businessplace, Green Beans and Ice Cream, gave the feature presentation on achieving excellence in HSSE at the 2022 Amcham HSSE conference at the Hyatt in Port of Spain.
He explained just how positive reinforcement could not only build a problem-solving team in a business but create a culture of excellence. Speaking to Amcham members and heads of industry, he applied this to the necessity of safety protocols in the workplace.
But nothing better illustrates the feasibility of a strategy than what happens when things don’t go as planned. People might not have noticed it, but Simms illustrated every aspect of his style of leadership, which he called PR+, when a small but significant piece of equipment malfunctioned – and threatened the timeline and flow of his presentation.
The clicker problem
Simms had a clicker problem.
Having 35 years of experience working with safety professionals, Simms left South Carolina at 6 am on Tuesday, drove to Charlotte, North Carolina, got to the airport there and flew to Miami, had a four-hour layover, then took a flight that lasted about another four hours, and arrived at the auditorium in the Hyatt to present – only to be standing in front of over 100 TT business and industry leaders with a busted clicker.
Without it he would not be able to navigate his slides for his presentation. The illustrations that he spent time and possibly money on to better explain his strategies would have to be left aside and he would have to give a reduced presentation.
It was a disaster – or at least it would have been for a leader who used the wrong strategies. A leader using an older module of leadership in safety would have stopped the presentation altogether and announced that his clicker wasn’t working. He might have admonished the staff and blamed them for giving him faulty equipment. He might have waited until another clicker was provided, which would have set back his time and the overall running time of the conference.
But instead, using his PR+ system, Simms seamlessly navigated the problem.
As soon as he noticed the clicker had stopped working, he called on the communications team, led by senior trade and projects officer Melissa Pierre. She charged one of her technicians, whom Simms called Joan, to navigate the slides while someone got another clicker.
During the first 20 minutes of his presentation you could hear him calling out to her to change the slides.
“Let’s get a click, Joan,” he would say.
Within a couple of minutes an usher walked across the auditorium and handed him a new clicker. Simms thanked him for bringing it.
“A round of applause for my knight in shining armour,” he said. “See you at the bar tonight for drinks on me.”
The crowd applauded the usher, who beamed as he walked back across the floor. The rest of the presentation was incident-free.
Simms explained that looking at the safety systems and protocols alone to assess whether a business place is safe will not leave leaders with a full picture of their HSSE frameworks. That strategy is part of the “safety 1.0” strategy.
“Safety 1.0 says workers are the problem you fix, you have to tell the staff what to do and what not to do to ensure that there is a safe environment for all in the area to work in, and safety is the absence of accidents,” Simms said.
“Safety 2.0 says that workers are not the problem, they are problem-solvers. You don’t tell the staff what to do, you ask them what they need. And safety is not the absence of accidents, it is the presence of capacity.
“So instead of preventing things from going wrong, safety 2.0 ensures that things go right.”
What makes a good leader?
Simms said great leaders can create a culture of commitment where people give more voluntary effort toward making a business more profitable, more productive and safer.
So what makes a good leader?
Simms said every good leader has mastered one superpower – the ability to use positive reinforcement to get the job done.
First of all, great leaders have to understand that work seldom goes as planned, Simms said.
He described a situation where everything goes as planned as a black-line workflow – where everything happens the way it is supposed to, everyone does what is required of them, there are no incidents and the job gets done.
“Some people believe that if everyone would just follow the procedure, no one would get hurt,” he said. “But does work always go the way that we plan it? Heck, no. Work is dynamic and fluid.”
On one day there may be a shortage of staff, on another day there may be a power outage or some other problem. Simms described this workflow as a blue-line workflow, which is a winding journey toward an end goal.
“Workers are masters of the blue line,” he said. “They can have all these variables and still achieve production.”
Another key factor Simms said leaders should consider is that there are different types of workers.
The first is the incompetent worker – the worker who cannot do the job. That worker may require training and guidance.
The second is the worker who knows the rules and protocols, but does not adhere to them.
The third is the worker who only does the right thing because he has to; and the fourth is the willing and committed worker who is doing what needs to be done because he wants to.
Simms said in order to change the results coming from workers, a behavioural change is needed. He said in most businesses, people rehearse for catastrophes.
But behavioural systems are a way to expand the capacity of staff for the event that if something does fail, it can fail safely without causing serious damage or even a fatality.
He also said a system should be put in place to measure the effect of positive reinforcement to ensure management is enabling the right behaviours.
“You have to be able to track positive reinforcement throughout your organisation. If you can’t measure it, then how are you going to be able to reinforce it?
This was where is theory of “green beans and ice cream” came in. He explained that when he was a kid, his mother would use the strategy on him to get him to eat his green beans. She would tell him if he ate all his beans, he would get ice cream after dinner.
“It worked,” he said. “I am eating green beans to this day.”
Why is safety important
Simms encouraged safety workers to continue their work, saying they were the last conscience of the business and industrial world.
He recalled a story told to him by a friend from Tennessee, who is currently working in Russia.
“I asked him, 'Why do you care about safety? Your family is in Tennessee. Why are you in Russia?”
His friend said he didn't, until his mother told him a story about his grandfather's experience in coalmines in the US. The mother sent his friend a black-and-white picture of a coalmine with four children standing in front of it. The mother told Simms' friend that every day, her father would go to work in the mine.
One day it blew, killing someone’s father. The mother said she ran to the mine and stood outside it, praying that her daddy would make it out of the mine. He did come out, and gave her a hug and a kiss and told her he was all right.
But her best friend from school was crying. It was her daddy who died in the mines.
Ultimately the father got another job out of the mine, but two years later he died from black lung disease.
“When you are a safety officer and you have to have uncomfortable conversations with people, are you worried what would happen? Are you worried that someone would punch you in the nose? Are you worried that you may lose your job, or are you worried that you may lose your life? I’ve known safety leaders that had all three happen to them,” Simms said. “Please don’t stop having those tough conversations.”
Simms said that safety workers not only ensure that businesses are protected, but also that every worker is safe and all families connected to that business stay together.
“No matter where you work – it could be a million miles away – there are little boys and little girls praying that their mommies and daddies come home. It is up to you to make that happen.”
Comments
"How positive leadership can revolutionise HSSE"